Aug 26, 2022
Re-Nuble Partners With Cruz Foam To Create Indoor Farm Nutrients From Seafood
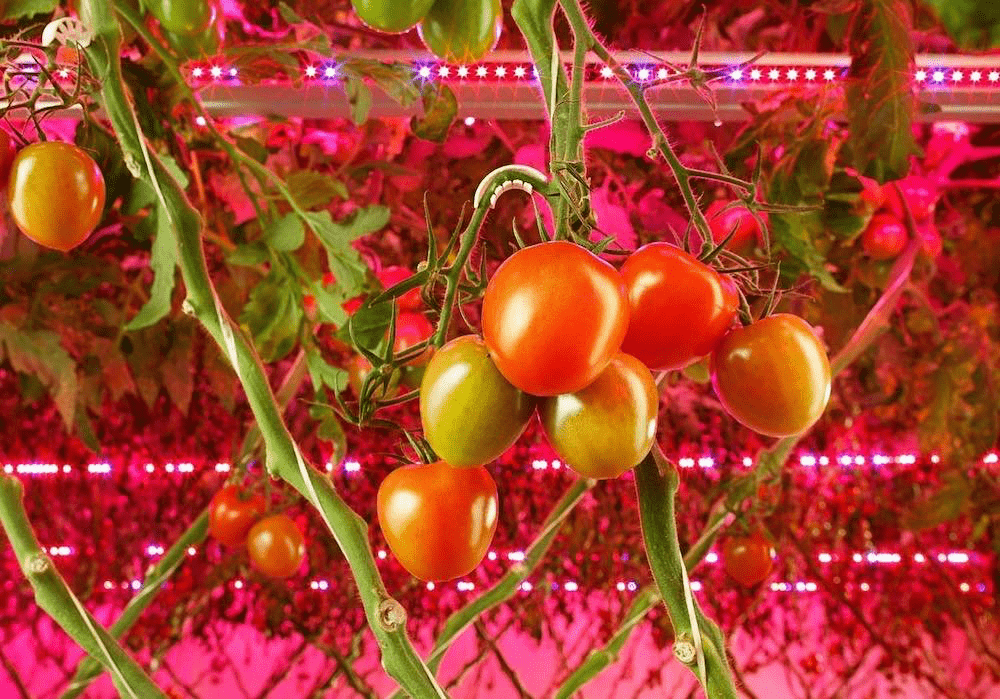
Indoor farming with Re-Nuble's sustainable grow-media | Credit: Re-Nuble
Editor’s Note: According to Nature’s research, “every year, some 6 to 8 million tonnes of waste crab, shrimp and lobster shells are produced globally. More often than not, this waste is burned, land filled, dumped at sea or left to get spoiled, creating additional environment and health concerns. It’s great to see Agritecture client Re-Nuble partnering up to curb this wastage from seafood operations, and we hope to see this work accelerate circularity industry-wide.
CONTENT SOURCED FROM AGFUNDER NEWS
Written By: Lucy Ngige
Re-Nuble is on a mission to upcycle a portion of the nearly 1.3 billion metric tons of food wasted annually. The New York-based company, which produces nutrients from organic waste for indoor farms, is partnering with another circular economy startup, California-based CruzFoam, to curb wastage from seafood operations.
CruzFoam, which recently onboarded actors Leonardo DiCaprio and Ashton Kutcher as investors and board advisors, produces green and sustainable packaging material from shrimp shells that are discarded by the seafood industry. The partnership will enable Re-Nuble to integrate some of this seafood waste into its farm-nutrient production cycle.
“We felt [CruzFoam] would be a good partner because they’re very aligned from a circularity perspective,” Re-Nuble’s founder and CEO Tinia Pina told AFN. She praised the company in particular for its transparency and respect for processes.
That kind of alignment is critical for accelerating circular, waste-to-value systems, where early-stage startups like Re-Nuble and CruzFoam recognize that they can be only one part of the solution.
Pina realized the extent of the food waste problem volunteering for social support nonprofit New York Cares in New York City. The city was spending tens of millions of dollars annually to dispose of food waste that Pina recognized could have numerous other uses if up-cycled or composted. She started Re-Nuble and bootstrapped years of research and development into how to use food waste for indoor farming media.
“Our team had a strong conviction that there was going to be a shift towards more indoor production because of what we’re experiencing now,” she explained. “The high temperatures, the erratic weather patterns, things that are limiting soil production. We really were a little bit ahead of the curve back in 2015.”
Fork to farm
Re-Nuble sources its feedstock from wholesale produce distributors as well as waste haulers and logistics providers. It also works with local companies and organizations to acquire their food waste.
The waste then goes through a proprietary process to be transformed into nutrients.
With its 6,300-square-foot manufacturing facility, Pina says Re-Nuble is able to produce 50,000 gallons per month of its liquid organic hydroponic nutrient product, which the company sells directly to indoor farms, including greenhouses and vertical farms. It is also sells its product to retailers that reach consumers.
“Shipping grow-media from other parts of world is not sustainable. We solve that by using localized waste streams, and through our business model, we are able to replicate this production process anywhere in the world,” she says.
Expanding range and reach
Re-Nuble’s plans to expand into new types of waste is part of a growth strategy made possible by its seed funding round, raised last December. With CruzFoam, the company will have access to seafood—specifically, shellfish—waste streams that can improve and expand its product line.
Pina noted the benefits of the polysaccharide chitin, found in shellfish and insects’ exoskeletons, in boosting plants’ resilience to some forms of pest and disease, for example.
The partnership with CruzFoam will also help Re-Nuble access a wider market and new agrifood industries, such as hemp.
Ultimately what Pina and Re-Nuble want to accomplish goes beyond stemming food waste: it’s to relieve indoor farms of their reliance nutrients procured on environmentally-hazardous processes, like peat harvesting.
“While several grow-media options exist for indoor growers, the industry lacks a truly sustainable form of grow-media,” says Pina. “There is an urgent and dire need to develop a fully compostable grow-media solution.”