Jan 19, 2022
How Converting An IKEA Parking Lot Can Feed Over 20,000 People

Rendering by RAND Engineering & Architecture
Editor’s note: The following information is derived from an interview Agritecture conducted with Eugene Gurevich, Senior Structural Engineer at RAND Engineering & Architecture, as part of Agritecture Studios. This first virtual Agritecture Designer cohort supported architects with a deep interest in urban agriculture who lacked the technical background necessary to move forward with their concepts confidently. Learn more about Agritecture Studios’ first cohort!
As the days pass, technology continues to advance at a rapid pace. And, with it, the built environment around us continues to age. With each technological innovation, we tend to be left with more man-made structures rendered useless.
One life-changing innovation that is soon to restructure cities and our everyday lives is self-driving cars.
With an autonomous vehicle future not too far out, what will become of all our parking lots?
This is the challenge Eugene Gurevich, Charles Huang, Ted Klingensmith, and Athmane Aouchiche of RAND Engineering & Architecture took on by participating in Agritecture Studios.
Where does fresh food fit into the equation?

Chosen site showcasing an aerial rendering of their farm model; Rendering by RAND Engineering & Architecture
Team leader Gurevich shares that “the COVID-19 pandemic has served as a catalyst for this shift in a number of impactful ways including a significant reduction in parking loads, inflations in the cost of food/fuel, and the mounting failures in our current just-in-time supply chain.”
With a background in sustainability design and consulting, he adds that “we are married to our aging built-environment and, in this finite world, a rebuild is unlikely. In this context, focusing our energy into the adaptive reuse of our existing infrastructure for local food production is worthwhile.”
The team adds that “with the emergence of autonomous vehicles (and widespread adoption of electric vehicles), the conversion of a large parking garage into an urban farm and distribution center would be an opportunity to accomplish many things.”
In order to do this as realistically and efficiently as possible, the RAND team set guidelines. First, they wanted to plan for the gradual and reversible conversion of a large parking facility into an urban farm. Second, they wanted this to be done with the most basic but customizable modular systems so that others could mimic the design for their sites. And, third, they wanted to amplify the philosophy of a world-renowned corporation with this project.
Bringing in the world leader of home furnishings, IKEA.
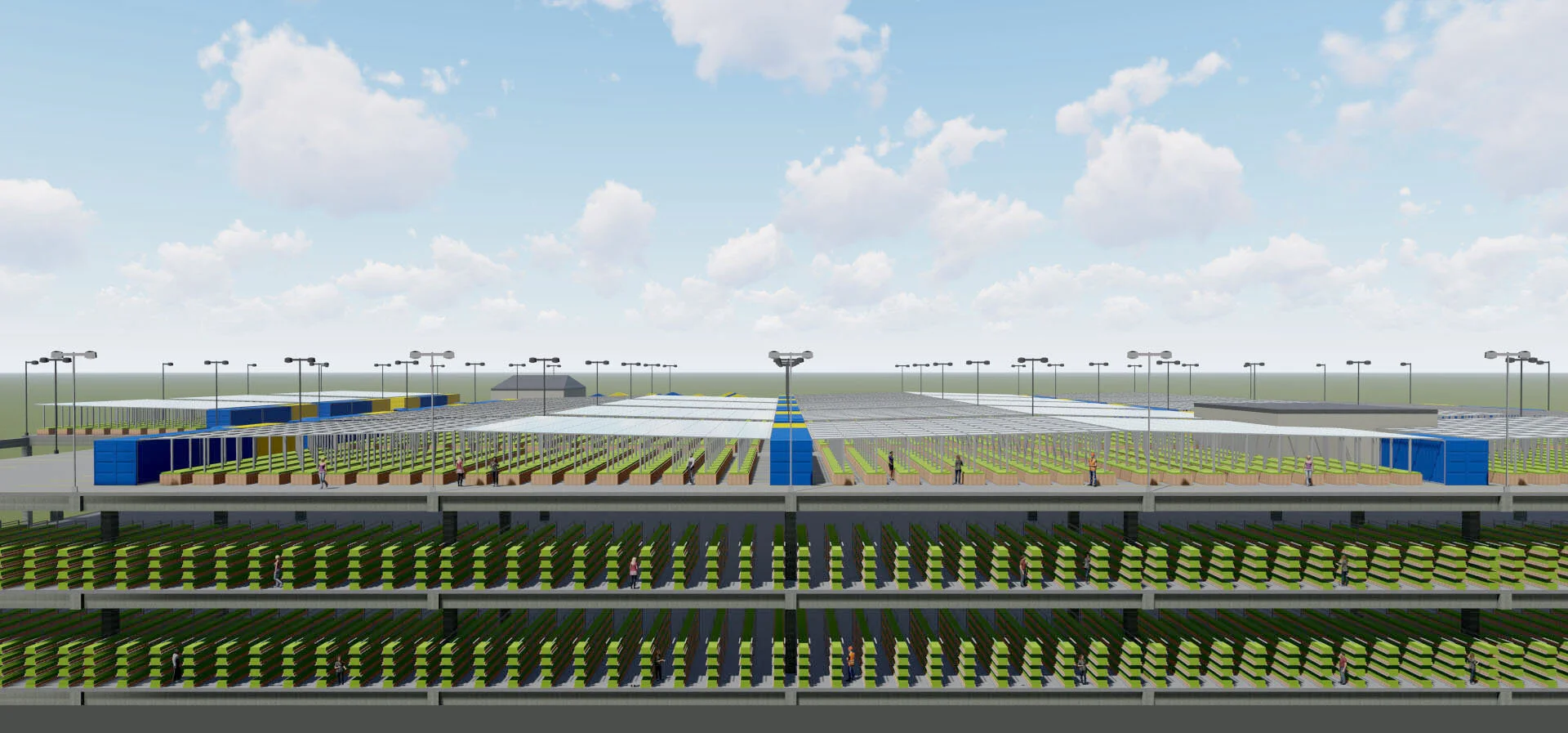
Rendering by RAND Engineering & Architecture
With the industry giant recently switching gears to vertical farming with their initial on-site hydroponic technology tests, the RAND team believed IKEA to be the best corporation to pitch this project to.
As a result, they settled on the IKEA parking garage in Paramus, New Jersey. Gurevich highlights that this site “was selected as the location of the proposed conversion due to its size, location, connectivity and proximity to major markets, accessibility,” and due to having “a variety of prospective indoor and outdoor spaces on the premises as well as an overall transformational potential as an extension of the IKEA brand.”
The 200,000 square feet facility features an expansive roof deck with ample south-facing exposure atop two floors of covered parking. With his structural engineering expertise, Gurevich shares that “the structural characteristics and parking dimensions are typical as prescribed by the applicable building codes and lend themselves to orderly conversion.”
How can controlled environments be utilized to produce food efficiently?

Rendering by RAND Engineering & Architecture
The RAND team considered both greenhouses and vertical farms on the premises.
The team envisions “modular temporary structures with light framing and corrugated plastic panels that could be easily assembled and disassembled by low-skilled labor, enclosed with free-standing shipping containers serving a variety of purposes including germination, washing/packaging, storage, farm stands, as well as complimentary vendors of various types.”
This basic model lends itself to high customization based on land size and owner needs without making any permanent changes to the site. For instance, the team intends to have rooftop photovoltaics in place on top of the containers for supplementary power. The sloped greenhouse roofs can be used to collect rainwater into cisterns. And, the farm site can easily be subdivided to grow flowers and support pollinators. Growing of vine crops such as tomatoes, cucumbers, and bell peppers is envisioned in these early stages.
The site is also expected to incorporate vertical farms “to generate income and increase overall viability.” The parking garage’s 15-foot high ceilings lend themselves to multiple grow levels (a total of four were assumed). “In addition to growing leafy vegetables, baby and microgreens via aeroponics in the early stages, this system would over time incorporate aquaponics growing of fish and shrimp, mushrooms, endives, as well as other profitable crops.”
In the more developed stages of the farm conversion, “the roof deck location is imagined as a large outdoor market with public squares and interior pedestrian corridors where customers can, in addition to shopping for groceries, spend an afternoon exploring the farm, dining, drinking, and otherwise enjoying the produce being grown feet away.” As a result, this model acts as a community hub, incorporating activities beyond food.
But, is this model viable?
The RAND team used Agritecture Designer to evaluate the viability of the evolving conversion in three phases, using a total of seven models in the software.

The team’s Agritecture Designer model considering the vertical farm’s financial overview
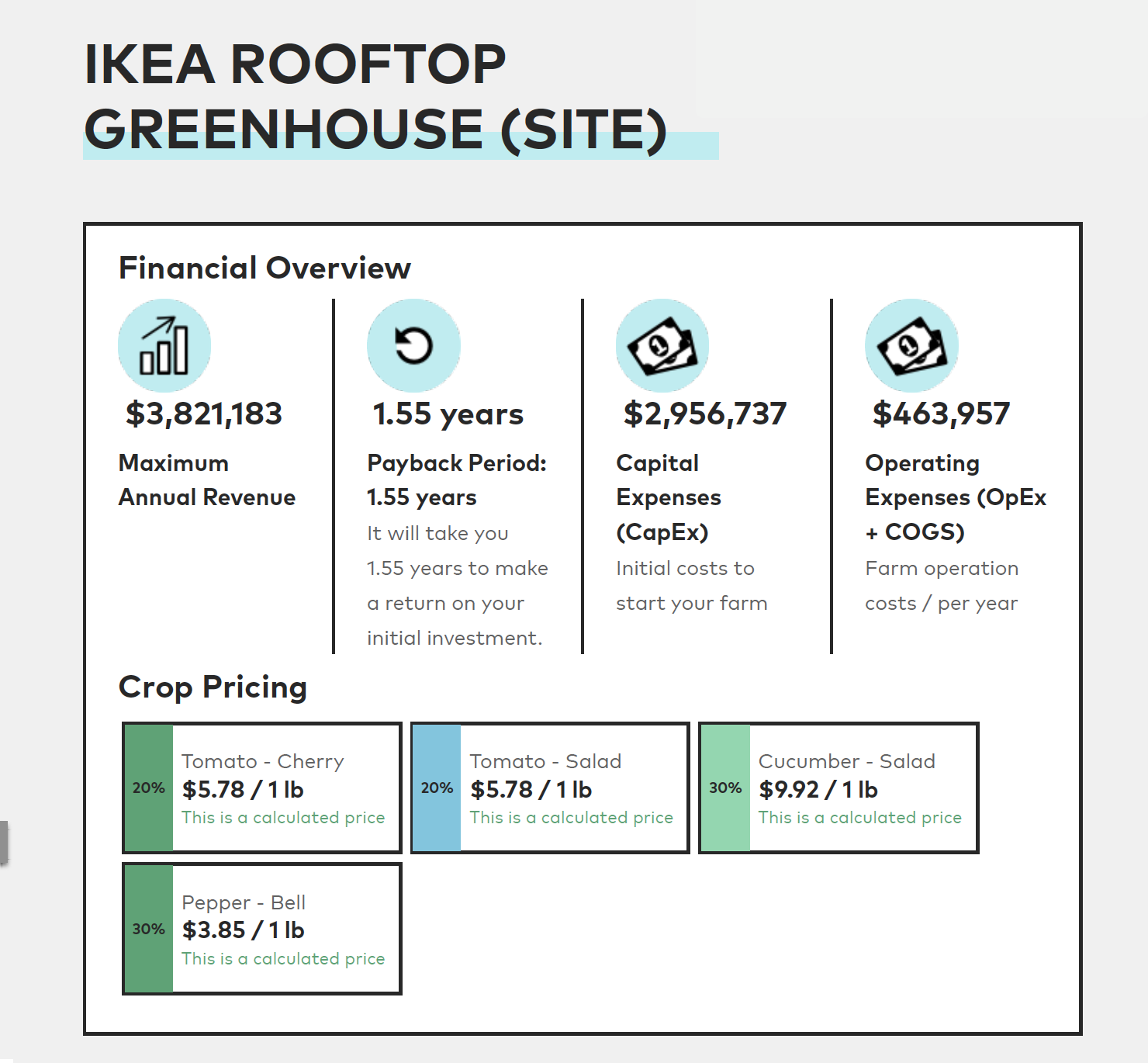
The team’s Agritecture Designer model considering the greenhouse’s financial overview
This three-part conversion model used crop prices based on market research of local grocers, supermarkets, and distributors, as well as typical farm startup and operating costs.
With this expanding model, the pilot farm is expected to feed 345 people with a maximum annual yield of 55,000+ lbs of produce. The second transitional farm is expected to feed 6,800+ people with a maximum annual yield of over 1 million lbs of produce. And the final “hub” stage is expected to feed over 21,000 people with an impressive annual yield of over 3.5 million lbs of produce.
The team comments that “based on these preliminary results, it appears the conversion of the IKEA Paramus garage into an urban farm can be a viable undertaking at every scale. While the vertical farming element lends itself to volume production for these types of facilities, the modular light-frame greenhouse assembly is of particular interest as it can, as envisioned herein, be applicable in any available lot and extend the local food production into residential areas by lowering the costs.”
With this data backing up the RAND team’s vision for an Autonomous Vehicle Future in partnership with IKEA, we’re excited to see how this project gets actualized. Get started with Designer today to make your urban ag dreams a reality!