Jul 16, 2020
The Critical Technologies That Sparked The CEA Revolution
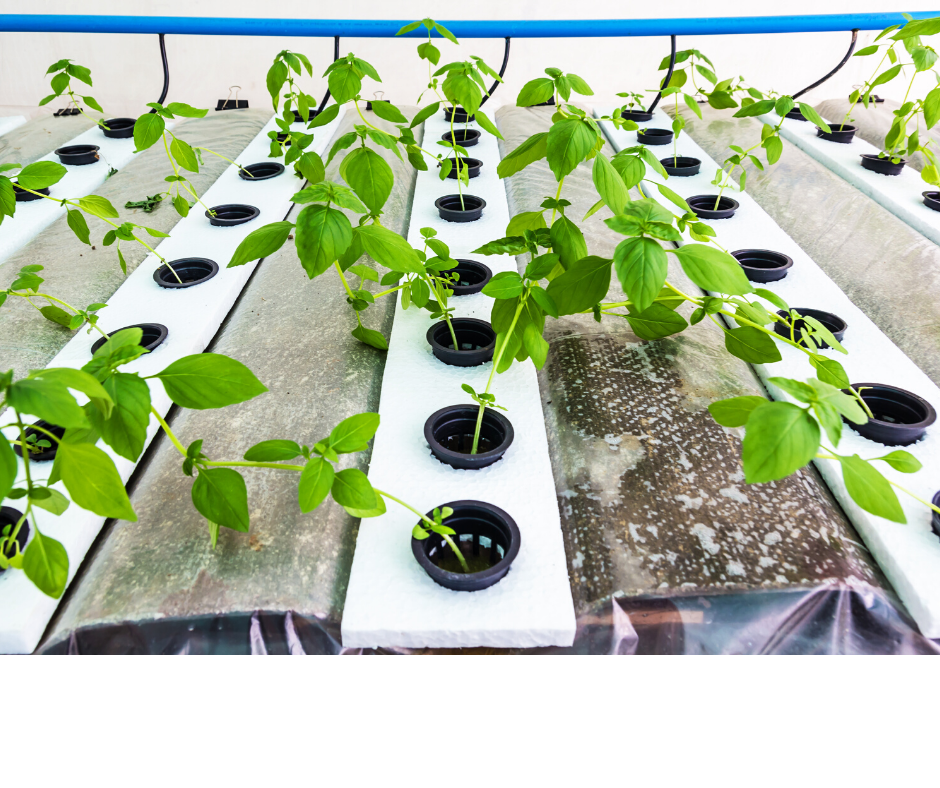.png)
Written By: Gene Giacomelli and Eric Roth
This is the second part of a two-part series looking at how CEA has emerged as a viable, contemporary agricultural practice over the past 50 years. Here’s how it happened. Read part one first!
Plastics
Polymer plastics such as polyethylene began providing a low-cost, energy-efficient film covering for greenhouses. This lowered the financial barrier to entry by creating more affordable greenhouses, thereby allowing unestablished growers to gain experience with a much lower investment than traditional glass-covered greenhouses. The plastic films dropped the investment cost significantly, while the more rigid, molded plastics improved operational metrics like production capacity, labor efficiency, and biosecurity.
Molded plastics also provided light-weight,easily-sanitized crop handling with trays, pots/flats, and clamshells for the packaging, among other things. Molded plastics further created light-weight structural channels, containers and benches which supported the plant and its root zone within hydroponic nutrient delivery systems, and even provided transport systems for improved labor and logistics management. Fully outfitted climate-controlled CEA plastic film boxes provided lettuce and greens production for the International Space Station.
Microprocessors
The microprocessor with its accuracy, consistency, data storage and simultaneous interpretation of multiple types and number of sensors has allowed the grower to tend more to plant production and much less to environmental control. No longer must the grower walk the greenhouse each morning to adjust the ventilation openings based on a guess of the day to be sunny, rainy or cold. Sensors are available to determine critical environmental plant needs and to make precise responses to air temperature and humidity for VPD (vapor pressure deficit) which affects plant transpiration and photosynthesis; light intensity with quantum sensors to determine DLI (daily light integral) which is directly related to desired growth or production rates; and, pH and EC which affects plant nutrient availability. When all combined, the grower is provided an improved understanding of the plant response to its environment. All this can be obtained on request in real-time by cellphone or within a report upon early morning arrival of the grower to the greenhouse each day.
Even more valuable is the capability of the computer to save data and further process it into useful information, which directs better grower decisions. Expect additional sensor development and implementation in the future to provide higher quality information about the food products, such as its flavor, sweetness, or nutritional quality.
The automation of information, although critically important, may become second in importance to labor-saving automation. Labor is often a farm’s biggest expense and the agricultural talent pool is limited nearly everywhere, but a high-tech farm’s food safety and security are dramatically enhanced when human contact with the edible product is reduced or eliminated. Production system automation that removes the need for people to work in groups on production lines is becoming crucial within this new world of viral pandemics.
There are still many advancements to be made in CEA. Technologies and experiences were transferred from the established greenhouse industry and applied to the developing indoor vertical farming industry. From LED lighting ‘recipes’ to plant nutrition under those recipes; from materials handling and logistics to labor management, years of R&D are required to reach optimal solutions for the plethora of combinations of plant cultivars, stages of growth, and harvest expectations within each type of CEA system.
The challenges remain for educating the people managing and operating the controlled environments. Educated employees working within a production process that is logistically sound, labor efficient, and task friendly are critical considerations for successful CEA businesses. Even with automation, the required work of skilled employees will remain, but at a higher educational level and a lower quantity.
In the future, it’s entirely possible that a CEA system will be able to autonomously program itself, or modify the plant environment without being directed, but for now, the plant production experience of an educated grower or crop manager is still required even in the most high-tech operations. Additional developments for successful CEA businesses include breeding of plant cultivars optimized for CEA production; emphasizing the importance of marketing; valuing employee education and experience; accepting that growing plants is a skill and an art; and, understanding basic physical principles that follow the laws of physics and biology!
CEA is still in such an early stage of commercial viability, but the blueprints for successful ventures continue to be created by intelligent and increasingly well-equipped entrepreneurs. As we look at the timeline of its commercial origins in Part 1, to the critical technologies that made it work, we can see how far it's come, but also the potential the future holds for feeding the world with controlled environments.