May 1, 2020
CEA Integrated System Analysis: A Perspective On Circularity
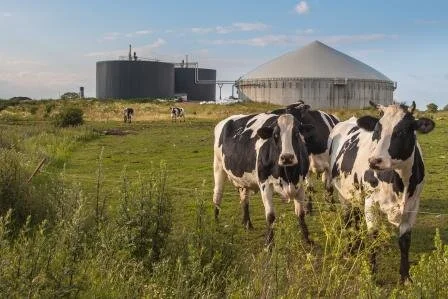
Written By: Alberto Lopez - Systems Engineer, Agritecture Consulting
If you research the term ‘Circular Economy’ you will come across many different definitions and explanations of this term. Some of the characteristics found across common definitions include the terms reduced waste, efficient use of resources, recycling of resources, and sustainable economic growth.
As I learned more, it became clear to me that the principles of the circular economy were closely related to the methodology used in Agritecture’s controlled environment agriculture (CEA) design. At Agritecture, our goal is to design economically feasible solutions while considering the environmental impact of the food system. This linkage made me think of what an integrated circular agricultural system should look like, and how it can achieve a sustainable balance between economic, social, and environmental aspects.
In this concept, CEA is taken as a subsystem; part of a larger system. This subsystem will be coupled via inputs or outputs to other subsystems. We assume that if the efficiency of the use of resources is increased in any of the subsystems, the efficiency of the whole system should increase as well. To achieve an optimal system size, the key is to identify “wicked links” (couplings of desired effects and unwanted side effects) and reduce synergetic bottlenecks (lack or surplus of internal system inputs) between subsystems. The following theoretical exercise is a general system analysis of an agricultural circular system and an explanation of the possible interactions.
Concept definition
Over the years, I worked on the operations side of a microgreen vertical farm in Amsterdam, where I had to test every new product request from our customers. The methodology for new product assessment was simple: general market price analysis, 2 to 3 months life-cycle testing, refinement of growing conditions, assessing the cost of production, and finally, volume and profitability definition.
I paid special attention to the number of resources that each product needed to grow. Setting aside the market value, a product with a short life-cycle will require fewer inputs to grow per square meter and will most likely be more profitable due to the number of harvests per year.
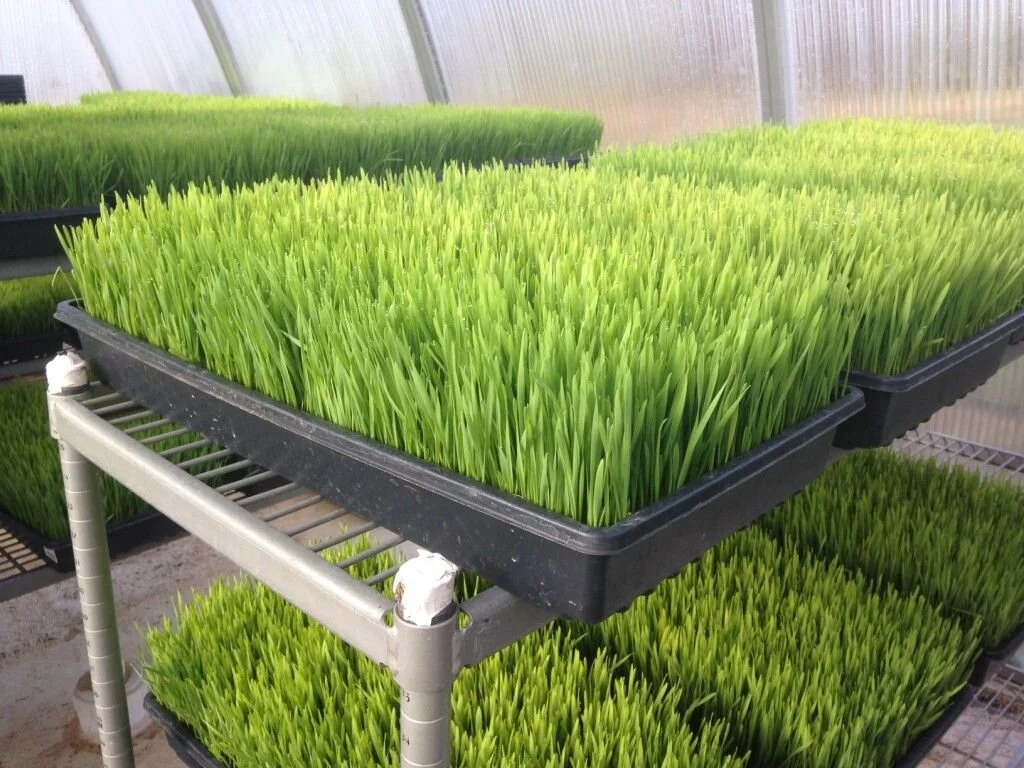
When doing this analysis for wheatgrass, it can be perceived as perfect to grow indoors. Under certain conditions, wheatgrass can grow from seed to a standard microgreen size in around 6 days with very low input. Since the roots develop thick and fast, it can be grown without substrate at a very high density. Based on my former experience with the product, I determined that for certain market conditions it does make economic sense to produce and sell to high-end restaurants, but can it be integrated into a semi-closed loop? What does a circular production of wheatgrass actually look like?
System description and interactions
The inputs of an indoor production for wheatgrass are seeds, energy (for lights and climate control), water, the packing materials needed, and carbon dioxide (CO2). The outputs are excess water from the pre-germination process, the harvested material, the inedible part of the crops, and heat from the climate control unit. Since it is a closed-loop water system, the transpiration of the plants is condensed in the cooling equipment and reused in the indoor production space.
The harvested material goes through a quality control process for human consumption and is then separated and designated as sellable and non-sellable. The sellable product is packaged and sent to the customers, the non-saleable product is disposed of.
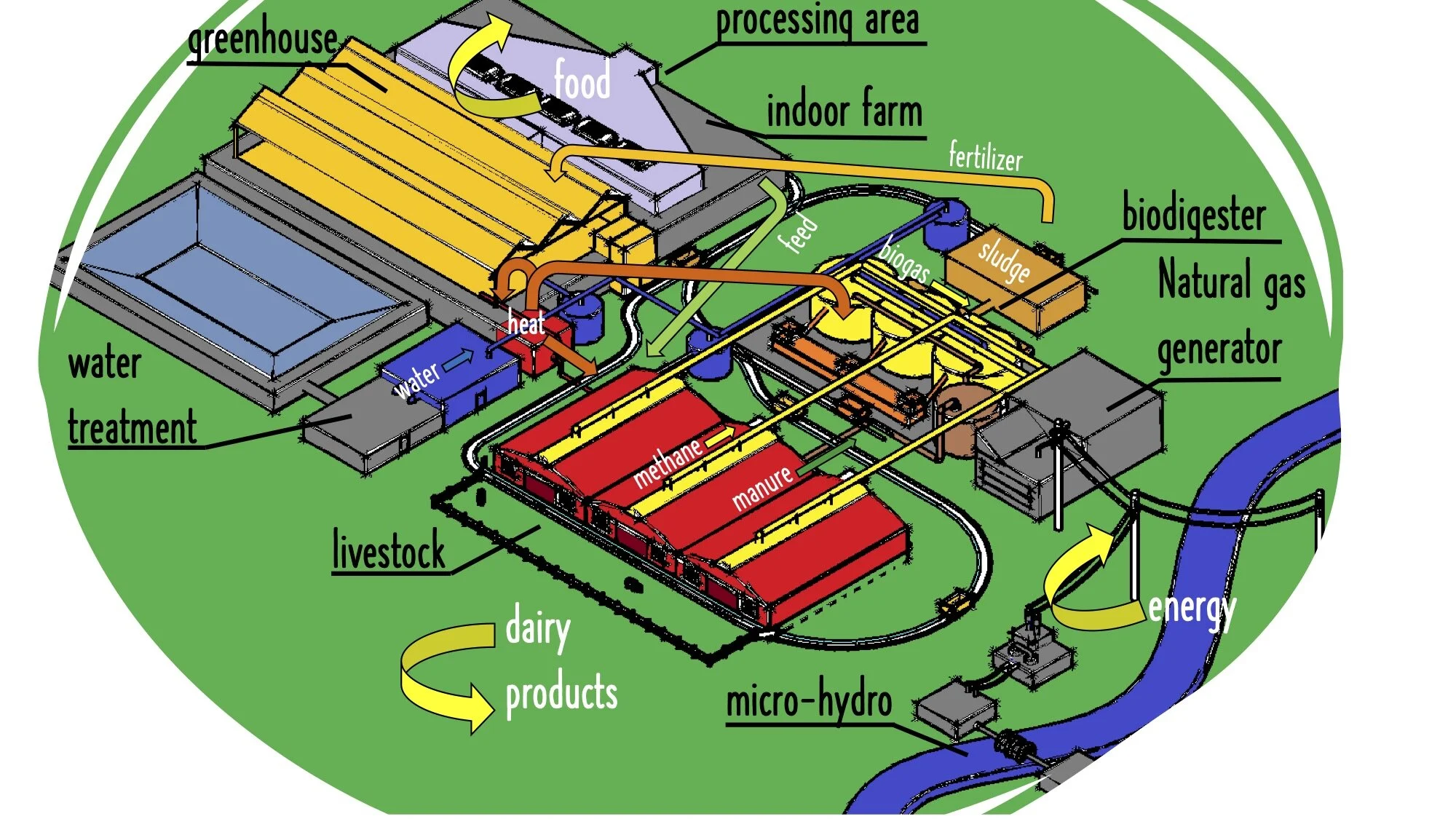
Here we can identify three waste streams: the used water, the biological material, and the heat. An alternative to dealing with these waste streams is to use them as inputs for a digester, and as a result, produce biomethane.
The inputs for a biodigester are heat, water, and organic matter with high volatile content. Bacteria break down the organic matter, producing methane through anaerobic fermentation. Although the waste material from straw can be used directly in the biodigester, a higher content of volatile solids can be found in animal manure. There is also the alternative of using co-digestion, which involves using as an input a mixture of manure and other plant material. In some studies, this resulted in steadier conditions for the bacteria to produce methane, with the potential trade-off of producing a less energy-dense output.
A new synergy can be added to the system by coupling a stall milk production facility. The inputs for this system are nutritious feed (can come from indoor production waste stream), heat, and water for the animals. The outputs include the manure, milk, and additional methane from the cows. The inclusion of this sub-system increases the total environmental impact due to cow methane emissions. The level of efficiency in this subsystem will be assessed by the strategies to mitigate cow methane production.
The manure produced in this subsystem will be fed to the biodigester along with the water waste stream from the indoor production. The outputs of the biodigester are the raw methane (which contains carbon dioxide, water, and small amounts of hydrogen sulfide) and the excess sludge which is very rich in nutrients and usually dried and used as fertilizer.
The methane can be purified via a carbon activated filter or water washing method (among other methods). As the gas comes out warm, a passive condensing pipe can be used to extract the water vapor from the gas. The CO2 extracted from the purification stage can be reused in the indoor farming sub-system to promote growth. The CO2 produced from a gas-powered electric generator can be used for this as well.
System boundaries
The system boundary defines what elements are part of the system and the flows in and out of it. In theory, a circular system should not have in or out flows, however, it depends on where the system boundary is set.
In the previously described system, the sub-systems included are indoor production, milk production, and biogas production. The inflow of resources includes the seeds for the indoor farm production, and to less of an extent, energy, and water. As an example of strategies to create a near closed-loop energy cycle, the system can include a micro-hydroelectric plant, which can supply power to production using a renewable method. Since the system only considers the production of the goods and not the consumption, outflows will always exist. The water flow will always have to be replenished due to the fact the final product of the indoor production sub-system is made up of around 50% water.
System considerations: Importance of scale
The outputs of the system that produce an economic benefit are the harvested wheatgrass, milk, and the fertilizer product of the bio-digestion process. We can also consider methane or energy as one of these outputs if the economic strategy is to reintroduce it to the grid. Here is one example where the scale of the total system comes into consideration.
The system design must consider the correct amount of inputs and outputs of each of the subsystems thus defining the resource use efficiency of the system. In the case described above, it will have defined parameters such as the area of wheatgrass production per cow, which would be related to liters of milk produced and cubic meters of methane obtained for energy production.
This gives insights that help us think outside a single integrated system and make available the horizontal coupling of several circular systems, which in turn, allows the inclusion of other subsystems never considered before. A resource efficiency analysis will tackle specific trade-offs, for example, if the inclusion of animal feed (external input) will increase the quality of the manure, decreasing the emissions from the animal and increasing the methane production from the biodigester. This is possible if a greenhouse production system can be added inside the boundary, which involves redirecting the heat and fertilizer streams.
Conclusions
The aim of an integrated (semi) closed-loop agricultural system is to achieve a sustainable balance between the economic, social, and environmental aspects of production. As we explore a given system, the strategies to achieve this balance involve, among others, the increased circularity and durability of relevant inputs throughout the system, the increase of the value of the outputs by transformation, and the availability of horizontal couplings with other systems. These paths can be applied to any circular scenario, as long as there is a proper understanding of the system interactions, inputs, and outputs.