Dec 6, 2018
Vertical Farming Company 'Spread' To Open New, Larger 'Techno Farm' In Japan
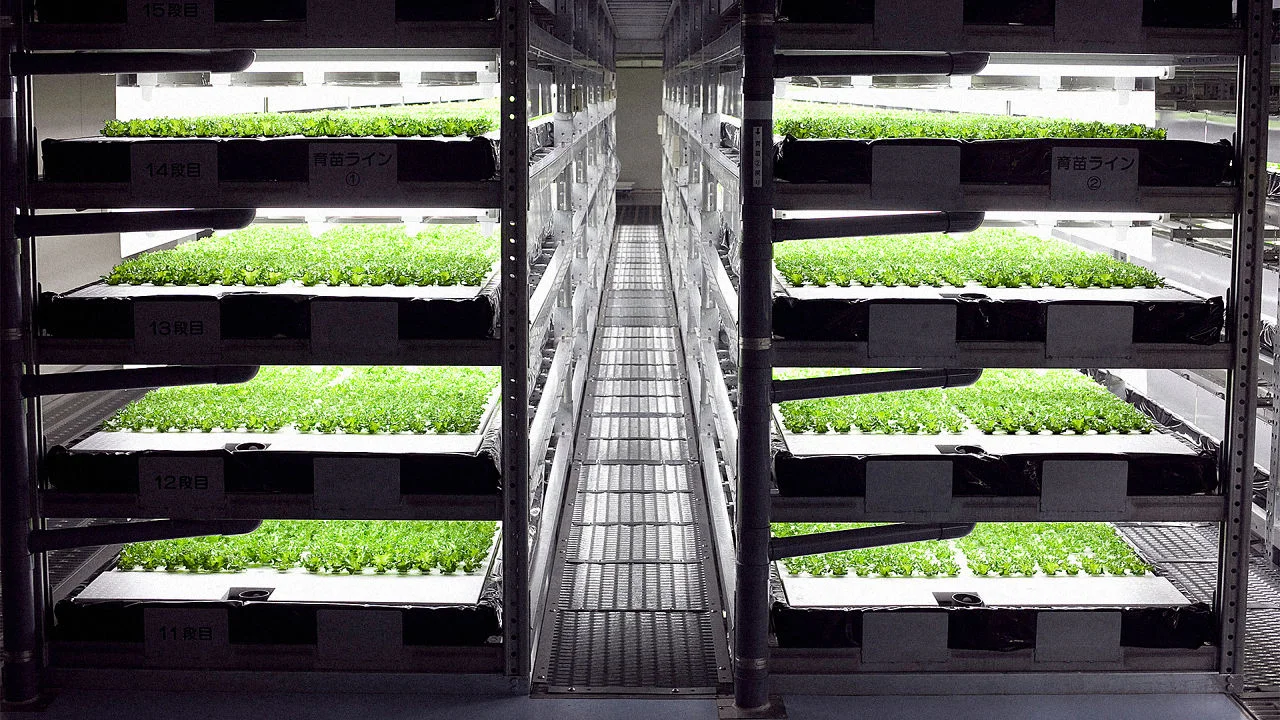
CONTENT SOURCED FROM THE JAPAN TIMES
As high-rise farms go global, Japan’s Spread leads the way.
In the hills between Kyoto, Osaka and Nara prefectures, surrounded by technology companies and startups, Spread Co. is preparing to open the world’s largest automated leaf-vegetable factory.
It’s the company’s second vertical farm and could mark a turning point for vertical farming — keeping the cost low enough to compete with traditional farms on a large scale.
For decades, vertical farms that grow produce indoors without soil in stacked racks have been touted as a solution to rising food demand in the world’s expanding cities. The problem has always been reproducing the effect of natural rain, soil and sunshine at a cost that makes the crop competitive with traditional agriculture.
Spread is among a handful of commercial firms that claim to have cracked that problem using a mix of robotics, technology and scale.
Its new facility in Keihanna Science City will grow 30,000 heads of lettuce a day on racks under custom-designed lights using light-emitting diode. A sealed room protects the vegetables from pests, diseases and dirt. Temperature and humidity are optimized to speed growth of the greens, which are fed, tended and harvested by robots.
Fixed Prices
“Our system can produce a stable amount of vegetables of a good quality for sale at a fixed price throughout the year, without using pesticides and with no influence from weather,” said Spread President Shinji Inada, 58, in an interview at the company’s first facility, in Kameoka, Kyoto Prefecture.
Inada won the Edison Award in 2016 for his vertical-farming system. He expects the new factory, called Techno Farm, to more than double the company’s output, generating ¥1 billion in sales a year from growing almost 11 million lettuces.
About 60 percent of indoor-farm operators in Japan are unprofitable because of the cost of electricity to run their facilities, according to the Japan Greenhouse Horticulture Association. Most others only turn a profit because of government subsidies or by charging a premium to consumers for vegetables that are chemical-free. Spread sells lettuces for ¥198 a head to consumers, about 20 to 30 percent more than the normal price for conventionally grown varieties, according to Inada.
Consumers pay the premium because the pesticide-free vegetables are increasingly seen as an alternative to often more expensive organic foods, which must be grown outdoors in soil. Japan’s hot summers and high humidity also make organic plants more vulnerable to insects and diseases, said Yasufumi Miwa, an expert at the Japan Research Institute.
“Producing organic vegetables requires extra-hard work by farmers and that should be reflected in the prices,” said Takumu Okuma, spokesman for online food supplier Oisix ra daichi Inc. “Pesticide-free vegetables are seen as safe by consumers and accepted by them as a substitute for more expensive organic ones.”
Small-scale vertical farms have been operating in Japan since the 1970s, predominantly as niche players that took advantage of high prices for fresh food in cities in a nation that imports about 60 percent of its food. But it wasn’t until 2010 that the sector began to expand rapidly, with the adoption of energy-saving LED lights and a government program to support innovative farming with subsidies, according to the association.
Spread’s Inada, a former vegetable trader, founded his company in 2006 and opened his first facility the following year in Kameoka. The company spent years refining systems for lighting, water supply, nutrients and other costs. The plant finally turned its first profit in 2013.

A worker examines lettuce at Spread Co.'s vertical farm in Kameoka, Kyoto Prefecture.
Techno Farm
Its new Techno Farm, expected to open as early as this month, will push efficiency further, yielding 648 heads of lettuce a square meter annually, compared with 300 heads at its Kameoka farm and only 5 in an outdoor farm. It will use only 110 milliliters of water a lettuce — 1 percent of the volume needed outdoors — as moisture emitted by the vegetable is condensed and reused.
Power consumption per head will also decrease, with the new factory using custom-designed LEDs that require about 30 percent less energy. A collaboration with telecoms company NTT West on an artificial intelligence program to analyze production data could boost yields even more.
Spread doesn’t disclose the cost of producing lettuce at its farms, but Japanese researcher Innoplex estimates the cost to produce one head of lettuce at its existing Kameoka building is about ¥80 — among the lowest in the world. The Japan Research Institute expects production costs at the new Techno Farm to come close to parity with outdoor farms within about five years.
But extreme weather events and climate change, major disrupters of traditional agriculture, are making vertical farming competitive even sooner. Japan’s hottest-ever summer this year, with its heavy rains, typhoons and flooding, sent supermarket lettuce prices soaring to more than double the level at which Spread sells its products.
Climate Change
“Climate change is affecting food production almost everywhere, and the economics of growing and selling produce is affecting everyone,” said Dickson Despommier, emeritus professor of Public and Environmental Health at Columbia University, who has been promoting the idea of vertical farming since the 1990s. “If we don’t do something soon to reduce the rate of climate change, vertical farming may be our last hope of getting food on the table for all those who live in cities.”
Around the world, many existing vertical farms are located in climates that are inhospitable for vegetable farming and have high transport costs to import fresh produce, or in places where pollution concerns created a demand for “clean” food, such as in China.
In Antarctica, where weather conditions prevents shipments of supplies for much of the winter, scientists at Germany’s Neumayer Station III harvested their first batch of indoor lettuce, cucumbers and radishes this year to feed the station’s staff. And in space, astronauts grow food on the International Space Station in a minifarm nicknamed Veggie.
Some commercial ventures have targeted wealthy nations in the Middle East as prime candidates for vertical farms because of the high cost of importing fresh produce. Dubai’s Emirates Flight Catering plans to begin construction next month of a 130,000 square foot (12,000 sq. meter) vertical farm to supply airlines in a joint venture with California-based Crop One Holdings. The $40 million facility is expected to deliver its first vegetables to airlines and airport lounges in December 2019.
Other high-rise farms have appeared in office towers or condos as part of the design. In Tokyo’s Ginza shopping area, stationery retailer Itoya tends a vertical farm on the 11th floor of its 12-story building to supply lettuces exclusively to its cafe, at a cost that would be uncompetitive with vegetables grown in outdoor farms.

Greenhouse Rivals
One of the biggest challenges to the wide-scale adoption of vertical farms is the rise of massive greenhouse-based operations outside cities that employ many of the same technologies — such as the U.K.’s Thanet Earth, which grows millions of tomatoes, peppers and cucumbers a year under glass. While these farms need more land, they harness natural sunlight, reducing power costs.
In Japan, where the workforce is aging and many companies have relocated production overseas, vertical farms can also be built in idled factories.
JX ANCI, a wholly owned subsidiary of JXTG Nippon Oil & Energy Corp., plans to build an indoor farm in its Narita plant by 2020, using Spread’s system. And Mitsubishi Gas Chemical Co. has agreed with Farmship Inc., a Tokyo-based startup established by a former Spread employee, to build an indoor farm that would grow 32,000 lettuces a day in Fukushima Prefecture.
The real race though, is to go global. Spread plans to export its farming system to more than 100 cities worldwide, competing with companies such as Crop One, U.S.-based and SoftBank-backed Plenty Inc. and Sanan Sino-Science of China. Inada said Spread has signed an agreement with a food producer in the UAE to supply its system, and is holding talks with about 300 other companies and researchers.
“We are targeting countries where fresh vegetables cannot be produced because of scarce water, extremely low temperatures or other natural conditions,” Inada said. “Our mission is to provide infrastructure for vegetable production to anybody, anywhere in the world.”